卒業研究のご紹介
2020年版
機械・自動車・ロボット系所属学生
小型全地形対応車の車体設計と製作方法検討
山口 大輝静岡県
創造工学部自動車システム開発工学科 2020年3月卒業
静岡県立御殿場高等学校出身
研究の目的
学生が自動車を設計・製作して競う大会として、全日本学生フォーミュラ大会(静岡県)、ソーラーカーレース鈴鹿(三重県)、ワールド・ソーラーカー・ラリー(秋田県)があります。その中でも全日本学生フォーミュラ大会は本学を始め多くの大学が出場しています。この大会はBaja SAEと言い、米国、韓国、中国、豪州、印度で開催されています。
本研究では、この車両の具現を目的に設計・製作を行います。1年目は海外大会で上位の成績を収める車両をベンチマークし、車体の設計をして、その製作方法を検討した後、製作に入り、治具の組み方などを検証します。
本研究では、この車両の具現を目的に設計・製作を行います。1年目は海外大会で上位の成績を収める車両をベンチマークし、車体の設計をして、その製作方法を検討した後、製作に入り、治具の組み方などを検証します。
研究内容や成果等
■ 設計
(1)規則と現状調査
Baja SAEのフレームはブレス(補強材)をフロントに入れるか、リアに入れるかによって、2種類の形状が存在する。参加車両の多くのチームがリアブレスを選択していることが判明した。リアブレスを選択する理由は、Baja SAE車両はミッドシップレイアウトとなっており、重量物がRRH(リアロールフープ)よりも後ろに集中するため、フロントブレスを選択した場合でも、リアにブレスを入れリア部分の強度を確保した形状とすることは必須条件となるため、リアブレスのみのフレームに比べ、重量が増加する。使用するエンジンが統一されているため、フレーム重量を考慮してリアのみにブレスを入れる形状を選択しているものと考えられる。
(2)デジタルモックアップ
2018年、アメリカ国内で3つ行われた大会のうち2大会で総合優勝し、年間チャンピオンを獲得したアメリカ、ロチェスター工科大学の車両をベンチマークとし各部分の検討を行った。ロチェスター工科大学の車両の写真から既に分かっている部品の寸法を元にしてフレーム各部の寸法を割り出し、その寸法をCAD(Computer Aided Design)に入力しデジタルモックアップを作成した。
(3)原寸大モックアップ
デジタルモックアップだけでは乗降性、視認性など不明確な点が多いと考え、塩化ビニール管を用いて原寸大モックアップの製作をした。完成したモックアップを使用し、各部の考察を行った結果、フレームを路面と干渉させないように前後の床面に角度をつけ、アプローチアングル、デパーチャーアングルを稼いでいる、ドライバー乗車部分のSIM(サイドインパクトメンバー)を曲げることでドライバーと周りのパイプとのスペースを確保している、といった工夫が見受けられた。しかし、曲げパイプの多用、角度をつけ溶接作業を行う部分が増加することは、パイプフレームを初めて製作する我々にはハードルが高いため、このフレームを参考にしつつCAD内で独自のフレームを設計しようと考えた。Fig.1 に実寸大モックアップを示す。
(4)車体設計
(3)で行った検討結果とBaja SAE Rulesを元にして車体設計を行った。設計上の注意点は以下の3点。①Baja SAE Rules に適合している。②できるだけ水平、垂直にパイプを配置し作り易くする。③曲げパイプを多用せず直線的に各ポイントを繋げる。その上でパイプに曲げの力を加えさせないようにパイプ接合点をフレーム各部のポイントに集中させ、入力された力が各パイプに分散していくことをイメージして接合点を決定した。
Baja SAEのフレームはブレス(補強材)をフロントに入れるか、リアに入れるかによって、2種類の形状が存在する。参加車両の多くのチームがリアブレスを選択していることが判明した。リアブレスを選択する理由は、Baja SAE車両はミッドシップレイアウトとなっており、重量物がRRH(リアロールフープ)よりも後ろに集中するため、フロントブレスを選択した場合でも、リアにブレスを入れリア部分の強度を確保した形状とすることは必須条件となるため、リアブレスのみのフレームに比べ、重量が増加する。使用するエンジンが統一されているため、フレーム重量を考慮してリアのみにブレスを入れる形状を選択しているものと考えられる。
(2)デジタルモックアップ
2018年、アメリカ国内で3つ行われた大会のうち2大会で総合優勝し、年間チャンピオンを獲得したアメリカ、ロチェスター工科大学の車両をベンチマークとし各部分の検討を行った。ロチェスター工科大学の車両の写真から既に分かっている部品の寸法を元にしてフレーム各部の寸法を割り出し、その寸法をCAD(Computer Aided Design)に入力しデジタルモックアップを作成した。
(3)原寸大モックアップ
デジタルモックアップだけでは乗降性、視認性など不明確な点が多いと考え、塩化ビニール管を用いて原寸大モックアップの製作をした。完成したモックアップを使用し、各部の考察を行った結果、フレームを路面と干渉させないように前後の床面に角度をつけ、アプローチアングル、デパーチャーアングルを稼いでいる、ドライバー乗車部分のSIM(サイドインパクトメンバー)を曲げることでドライバーと周りのパイプとのスペースを確保している、といった工夫が見受けられた。しかし、曲げパイプの多用、角度をつけ溶接作業を行う部分が増加することは、パイプフレームを初めて製作する我々にはハードルが高いため、このフレームを参考にしつつCAD内で独自のフレームを設計しようと考えた。Fig.1 に実寸大モックアップを示す。
(4)車体設計
(3)で行った検討結果とBaja SAE Rulesを元にして車体設計を行った。設計上の注意点は以下の3点。①Baja SAE Rules に適合している。②できるだけ水平、垂直にパイプを配置し作り易くする。③曲げパイプを多用せず直線的に各ポイントを繋げる。その上でパイプに曲げの力を加えさせないようにパイプ接合点をフレーム各部のポイントに集中させ、入力された力が各パイプに分散していくことをイメージして接合点を決定した。
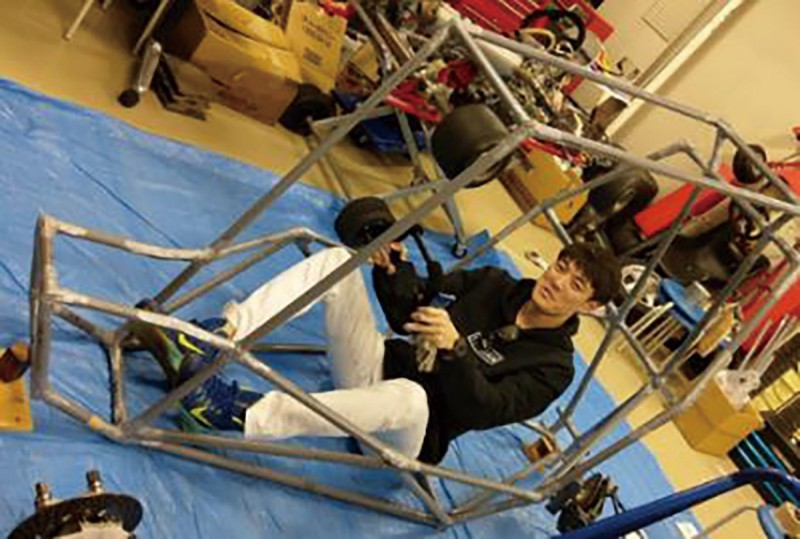
(5) CAE解析
Baja SAE のフレームは競技中のあらゆる衝撃から乗員を保護することが必要なため Auto desk Fusion360を使用して競技時に想定される前方衝突・後方衝突・側面衝突・横転・前方2輪からの着地・後方2輪からの着地、6項目のCAE(computer aided engineering)解析を行いフレーム変位量の調査を行った。車両重量は参加車両のベンチマークから250kg〜300kgと想定されるため300kgとし、参考としてインド、パンジャブ大学のフレーム報告書内で前方衝突・後方衝突・側面衝突・横転時は 4G(300×4×9.81=11772N)の荷重をかけ、前方2輪からの着地・後方2輪からの着地時はショックアブソーバー付け根部分に6G(300×6×9.81=17658N)をかけフレーム評価を行っていたことから同様の条件で解析を行った。変位が最大となったのは横転時の43.9mmであった。Baja SAE Rulesによって乗員の頭上は152mm、乗員の肩、胴体、腰、太もも、膝、腕、肘、手は76mmのクリアランスを確保することが定められており、変位量がクリアランス内に収まることを確認し解析を終えた。前面衝突の解析結果を Fig.2 に示す。
Baja SAE のフレームは競技中のあらゆる衝撃から乗員を保護することが必要なため Auto desk Fusion360を使用して競技時に想定される前方衝突・後方衝突・側面衝突・横転・前方2輪からの着地・後方2輪からの着地、6項目のCAE(computer aided engineering)解析を行いフレーム変位量の調査を行った。車両重量は参加車両のベンチマークから250kg〜300kgと想定されるため300kgとし、参考としてインド、パンジャブ大学のフレーム報告書内で前方衝突・後方衝突・側面衝突・横転時は 4G(300×4×9.81=11772N)の荷重をかけ、前方2輪からの着地・後方2輪からの着地時はショックアブソーバー付け根部分に6G(300×6×9.81=17658N)をかけフレーム評価を行っていたことから同様の条件で解析を行った。変位が最大となったのは横転時の43.9mmであった。Baja SAE Rulesによって乗員の頭上は152mm、乗員の肩、胴体、腰、太もも、膝、腕、肘、手は76mmのクリアランスを確保することが定められており、変位量がクリアランス内に収まることを確認し解析を終えた。前面衝突の解析結果を Fig.2 に示す。
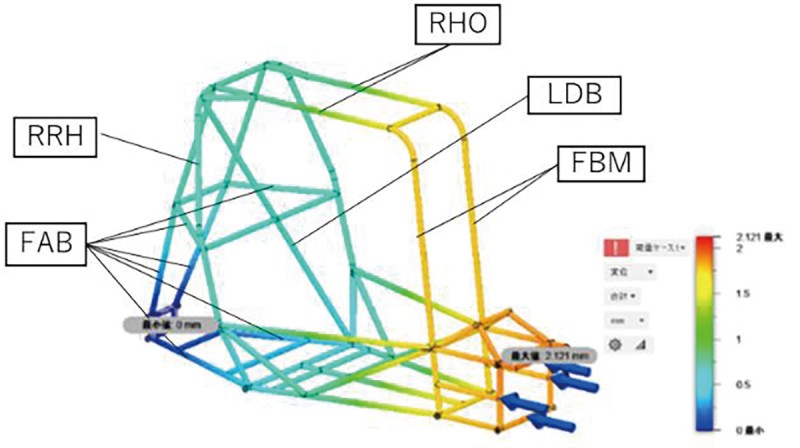
■ 製作方法検討
パイプフレームを制作する場合、フレーム形状に合わせて鉄板から切り出した各部分のパーツを溶接によってくみ上げて完成させた冶具を、フレームの全長・全幅よりも大きな定盤に固定して水平を出し、溶接作業を行う手法がある。しかしパーツ切り出し時、溶接時のわずかなずれ、それがフレームのずれに繋がり寸法精度の低下が考えられること、本学にある定盤は冶具を固定するための穴が半面にしかあいていないため、フレーム全体を固定することができないことなどが課題となり、新たな製作方法が必要となった。そこで足場部材を用いた製作方法の検討を行った。足場部材は組み換えがしやすいためフレーム形状に合わせて柔軟に形状を変えることができ冶具部材として活用できると考えられ、足場部材を使用することで以下のメリットがある。冶具を製作する手順を省けるのでフレーム製作にかかる時間を削減できる・冶具を固定するための定盤を必要としない、このことから足場部材を使用し車体製作工程の検討をCAD上で行った。Baja SAEのフレームはドライバーの上部にRHO(ロールフープオーバーヘッドメンバー)を配置することによりドライバーを箱の中に完全に保護するというのが1番の特徴である。そのためフレームを囲うようにして祭りなどで使用されるようなやぐらを建て、それを土台にして各パイプを上下前後から固定し溶接作業を行う方法を検討し工程図を作成した。車体製作工程の一例をFig.3 に示す。
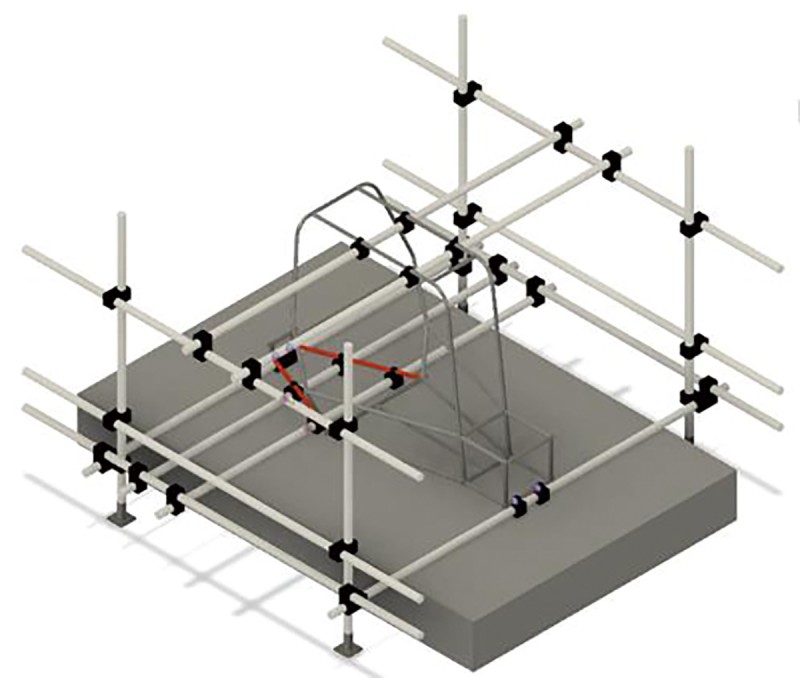
■ まとめ
本研究では小型全地形対応車の車体を題材としてこれまで一般化されていなかった設計から製作までの一連の流れを明らかにし、足場部材を使用した簡易的な治具の検討を行った結果、以下の知見が得られた。
1. 車体設計を行う上で経験がない学生が設計する場合有力チームの車体を参考とすることが一般的である。しかし複雑な構造で製作されていた場合、実際の製作方法を考慮する必要があると分かった。
2. 治具部材に足場部材を使用することにより、治具を製作する必要がないため車体製作にかかる時間を削減でき、定板を必要とすることなく車体製作を行うことが可能である。また立体的に治具を組むことが容易となりBaja SAE車体を製作する場合、使用しやすい治具部材である。今後、本研究成果に基づいて車体の製作を行っていく。
1. 車体設計を行う上で経験がない学生が設計する場合有力チームの車体を参考とすることが一般的である。しかし複雑な構造で製作されていた場合、実際の製作方法を考慮する必要があると分かった。
2. 治具部材に足場部材を使用することにより、治具を製作する必要がないため車体製作にかかる時間を削減でき、定板を必要とすることなく車体製作を行うことが可能である。また立体的に治具を組むことが容易となりBaja SAE車体を製作する場合、使用しやすい治具部材である。今後、本研究成果に基づいて車体の製作を行っていく。
-
指導教員からのコメント モータースポーツ工学研究室准教授 岡崎 昭仁
- 工学教育はモノづくりをすることに意義があると考えています。そもそも、『工学』とはモノを作るための学問領域です。山口さんは、3年次の目玉科目である自動車開発プロジェクトにて、国内では誰も作っていないBaja SAE向けのバギーを製作したいと希望しました。当人が自覚している通り、『言うは易く行うは難し』を感じてくれたようなので、教育成功かなと思ってます。本来、数人規模で設計、製作検討をする規模の内容なのですが、一人で黙々と来る日も来る日も図面を描いてました。勉強がてら真夏の暑い日に、一緒にジムニー博物館へ行き、調査した記憶が残っています。やがて、後輩がこの車両を完成させるでしょう。
-
卒業研究学生からの一言 山口 大輝
- 先ず、『言うだけならば簡単で実際に行うことは百倍難しい!』ということを実感しました。パソコンを使って図面を描けば、泉から水が湧き出るようにモノが勝手に出来上がると思っていました。図面を描きながら、どうやって作るかまで考えることが設計だと知りました。教室の講義ではこんなことは思ってもみませんでしたが、モノづくりを大切にする研究室で1年間を過ごし学ぶことができました。卒業後は自動車メーカーの関連会社で設計を行う予定です。研究室で学んだことはきっと役に立つと信じています。
- 創造工学部自動車システム開発工学科(大学サイト )
- 教員紹介ページ(大学サイト )
- 研究室ナビ(大学サイト)